培训时间:2016年10月13日 至 2016年10月15日
培训地点:上海
培训费用:5400元
培训讲师:刘宝生
标准作业工厂实践
培训费用:¥5400元/人(包括授课费、资料费、会务费、午餐等)
授课对象:各部门经理、生产主管、品管主管、工程师、班组长、精益经理、精益专员等 ;
--------------------------------------------------------------------------------
【标准作业是什么】
标准作业是以最少较少的工数(工时),生产出高品质的一种工作手法。是将作业人员、作业顺序、工序
设备的布置、物流过程等问题作最恰当的组合,以达到生产目标而设定的作业方法。标准作业的实施可
以确保装配和加工工序的品质。在不损害设备并确保安全的情况下,用更快捷有效的方式完成作业。
【培训目的】
通过培训向企业现场管理人员讲授标准化操作与工作研究技术,掌握优化生产现场的基本方法,减轻工人的劳动强度,降低生产成本,提高产品质量,最终提高劳动生产率的目的。
【课程作用】
提高生产效率
提高产品质量
保持改善成果
为未来的改善提供基准
识别和消除流程的变动性
目视化的核心内容
员工培训的教材
【导入契机】
在企业推行精益过程中遭遇以下问题时的有效解决方案:
开展了很多改善,但总是会倒退?
现场改善没有达到预期的目标?
员工离职后,改善被打破?
改善没有被员工遵守?
需要提高生产效率、产品质量?
还没有进行系统性改善?
【课程特色】
实践训练法,确保学员掌握技能,直接输出结果,培训模式采用互动小组讨论+沙盘模拟方式,确保培训效果最大化。40%理论:通俗易懂的、系统的阐述理念、工具、方法的理论体系;60%实践:教授小组到工厂现场观察流程、分析流程、找出问题和改进机会;指导小组实际运用工具、方法完成培训课题,培训结束产生收益;
【课程收益】
提高生产效率、降低在制品、节约空间;
掌握单件流布局方法;
掌握节拍控制和标准作业方法;
掌握生产线管控和绩效管理;
学会生产线可视化规划方法;
--------------------------------------------------------------------------------
课程大纲:
第一天
一、课程及团队建设
讲师自我介绍
培训的时间安排、内容大纲和注意事项
团队组建、团队介绍、团队期望
二、精益生产系统
精益的概念及含义
丰田生产系统:
◆一个中心(顾客)
◆两大支柱
·自动化概念及运用
·准时化含义及运用
→准时化三大要素
◆节拍概念及计算
◆单件流
◆下游拉动
◆三大地基
·标准作业
·均衡生产
·持续改善
精益生产的核心和精髓
为什么要精益生产
三、标准作业概念及意义
标准作业概念
标准作业在精益生产系统中的地位
标准作业的作用
标准作业三要素:
◆节拍时间
◆标准作业顺序
◆标准在制品
标准作业改善步骤
四、现状流程分析
现状流程分析
◆作业流程分析
◆标准工时测量
现状绩效统计
◆小时人均产出
◆在制品库存
◆空间占用
◆质量合格率
五、七种浪费讲解
七大浪费概念及案例
◆过量生产
◆库存
◆等待
◆搬运
◆多余工艺
◆多余工作
◆反攻
浪费产生的原因
六、现场浪费实践
小组现场发现浪费
浪费及问题分析
问题总结分享
第二天
七、生产线优化讲解
节拍概念
生产平衡率计算
生产平衡率提升方法
◆生产效率提升四大原则ECRS
生产效率的体现形式
八、标准作业沙盘模拟
传统流程运作模式
传统流程的绩效和问题总结
模拟优化方案讨论
◆布局优化
◆流程优化
◆工序平衡优化
◆人员优化
优化方案沙盘
九、生产线优化案例及方法总结
实际生产线优化案例
生产线和工位规划原则
实际工位设计讨论
十、实际生产线优化方案讨论
节拍时间设定
生产线布局
工位、及工装规划思路
产线平衡方案
改进目标设定
十一、优化方案分享和优化
各小组分享
点评
方案优化
十二、改进行动计划
各小组改善项目和方案
具体项目负责人
具体项目完成时间
需要支持事项
十三、总结
第三天
十四、生产线优化现场实施
现场布置(新流程布局、物流配送规范)
流程及运作规划说明
◆员工说明会
现场实施观察
◆运行细节完善
十五、现场问题分析
现场问题分析
现场问题解决
后续解决方案制定
十六、完成标准作业表、完善可视化
标准作业讲解
制定实际标准作业表
制定可视化完善方案
十七、建立异常处理机制
异常因素讨论
◆生产要素人、机、料、法的异常
异常应对策略和流程
十八、现场运行跟踪
现场运营跟踪
问题分析与解决
绩效统计
十九、总结及后续行动计划
各改善小组改总结
◆现状分析过程
◆解决方案形成过程
◆改进过程
◆改进成果总结
◆改善学习体会
后续问题解决对策和计划
后续改善行动计划
--------------------------------------------------------------------------------
讲师介绍:刘宝生
曾任:
全球改善咨询集团中国区顾问总监
奥曼克咨询有限公司精益首席顾问
摩托罗拉移动通信公司生产经理/精益经理
福特江铃汽车股份公司物流规划工程师/精益项目经理
教育及资格认证:
首席顾问、世杰精益学院院长;上海交大总裁班受邀讲师、惠普大学特聘讲师;曾任全球改善咨询集团中国区顾问总监、上海某咨询有限公司项目总监、摩托罗拉移动通信公司生产经理、精益经理福特江铃汽车股份公司、物流规划工程师/精益项目经理等职位;
讲师经历及专长:
实战派精益生产专家,十年精益生产推行实践经验,先后在世界五百强企业福特江铃汽车、摩托罗拉担任物流、生产经理、培训师等职位,全面推动上述公司中国区精益生产实践工作,在缩短周期、提高效率、降低库存等方面取得卓越成就。赴日(丰田)学习TPS,并与顶级TPS顾问一起工作。
作为高级咨询顾问,专注于精益生产的咨询和研究,积极探索中国企业的精益变革之路。专注于对重大咨询项目的整体控制和资源协调。他与那些注重结果,希望通过顾问服务提升生产效率和产品的客户紧密合作,并得到他们的高度评价。
历任上海大知项目总监,全球改善咨询集团中国区顾问总监,上海交大总裁班受邀讲师,为数十家企业提供精益生产咨询项目服务,为数百家客户提供培训服务,受训学员超过万人。
咨询:秉承谦虚、务实的作风,深入了解客户流程和文化特点,为客户提供个性化、针对性精益生产解决方案,提倡“教练式”咨询方式、“实践性”培训方式,在实践中训练和提升客户团队的精益技能,培训客户内部能力和人才。
培训:刘老师力求将精益变得简单、通俗易懂,咨询,刘老师力求实践,启发大家在实践中找到答案。多年实践经验总结,欣慰的是每次客户的肯定和认可,“痛并快乐着”的精益之路,是刘老师一生的职业追求。
部分培训咨询客户:
按行业特点划分:
汽车及零部件行业:延峰伟世通汽车电子有限公司、麦格纳动力总成有限公司、上海海拉电子、大陆电子集团有限公司、北京汽车、福特汽车(南京)有限公司、神龙汽车有限公司通用电器上海有限公司、上海大众汽车有限公司、蒂森克虏伯(长春)转向柱有限公司、双钱载重轮胎有限公司、佳通轮胎有限公司、上海比亚迪汽车有限公司等;
大型装备及机械制造行业:利勃海尔机械(大连)有限公司、上海三一重工科技有限公司、沈阳机床、上海沃尔沃建筑有限公司、佳木斯煤机集团有限公司、日本工装自控工程无锡有限公司、无锡威华机械有限公司、百士吉泵业、宁波伊顿液压有限公司、亚萨合莱系统(上海、苏州)有限公司锡兰瓦船舶有限公司、梅西埃航空苏州有限公司、常州法力诺钢管有限公司、常州腾普精机有限公司、常州法力诺钢管公司等;
家电行业:广州飞利浦中国有限公司、杭州松下电器有限公司、泰尔茂医疗、上海科勒有限公司、中国海尔集团、重庆格力电器、马尼托瓦餐饮设备公司等;
电子通讯行业:惠普电子、东莞诺基亚通讯有限公司、南京爱立信有限公司、西门子听力仪器苏州有限公司、南京索爱有限公司、广东比亚迪电池股份有限公司、杭州东芝信息科技有限公司、;斯比泰电子有限公司等;
化工及制药行业;上海施贵宝制药有限公司、罗杰斯科技(苏州)有限公司、欧文斯科宁复合材料(杭州)有限公司、诺维信中国、上海罗氏制药有限公司、杭州泰尔茂医疗有限公司、北京中化集团、上海双鹤药业有限公司等;
食品及饮料:南京卫岗乳业有限公司、上海太太乐食品有限公司、哈尔滨三精制药有限公司、内蒙古伊利集团、宏达集团、顶津食品、加多宝集团、北京荷美尔食品等;
其它行业:贵州电信、嘉兴民丰特纸股份有限公司、上海惠尔美箱包等;
报名方式二:点击这里 填写报名回执表,然后点击打印按钮打印出来,传真到:(020)82694022或(0755)61286566或(021)51697912即可完成报名流程。 |
金牌讲师
更多 >>
按培训分类浏览

相关培训
- [深圳 10/27] 制造型企业全面质量管理(TQM)
- [深圳 10/28] 几何尺寸和几何公差
- [深圳 10/28] 全面现场质量管理TQM与CI持续改善
- [上海 10/28] 品管七大手法(QC7道具)
- [深圳 10/29] TQM全面质量管理与CI持续改进训练班
- [深圳 10/29] “零缺陷”质量管控实战训练
- [广州 11/4] 质量零缺陷与TQM全面质理管理
- [江苏 11/8] SPC&MSA;
- [广州 11/10] 品管七大手法(QC7道具)
- [上海 11/11] TQM-全面质量管理
- [东莞 11/11] GD&T;形位公差与尺寸链计算
- [上海 11/11] 质量零缺陷与TQM全面质理管理
- [广州 11/12] 现场质量五大工具研修班
- [杭州 11/16] 防错防呆技术及其最新技术
- [上海 11/19] 新旧QC七大手法课程教案

博越主办培训现场剪影
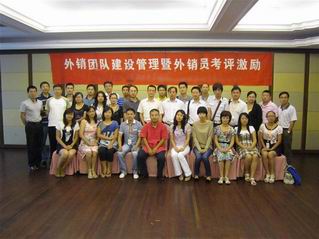






